Intralogistics has developed significantly in recent years, from a "cost center" to a real value creator in companies. Companies that serve their customers faster and more reliably gain a clear competitive advantage. A major factor in the performance of logistics centers is the employees; they know how to deal with the non-linear business, daily fluctuations, and technical challenges. While staff flow is a core process in logistics centers, they are a major TCO factor, and poor or unbalanced utilization means a massive waste of hours.
1. Personnel flow is a core process
Logistics centers are complex and expensive systems, both to purchase and to operate. Highly automated systems attempt to increase performance and make material flow processes more comprehensible, effective, and efficient; however, this comes at a price, e.g. in the form of flexibility. Logistics centers are built for specific use cases and load behavior. Once built, they can only be adapted to changing conditions with great effort; fixed automation is inflexible. The last few years have shown that environmental factors change use cases and load behavior. Customers change their purchasing behavior in the short or long term, supply chains change, or a company changes its business model altogether, e.g. by changing its sales channels. In addition, the purchasing behavior of end customers is difficult to predict in many industries. Forecasts are rarely accurate. The most flexible "resource" in the warehouse is the people. They know exactly what to do if 10,000 more orders arrive than planned, or if several carriers arrive too early, too late, or not at all, or if technical challenges weaken the warehouse.
2. Employees are costly and hard to find
Although employees are the most flexible resources, they are a costly investment and sometimes very difficult to find. In addition, there are labor law and trade union framework conditions that make flexible work deployment difficult and prevent performance-related incentives. In many European countries, employees are paid according to a fixed, hourly working time model and not according to the volume processed in the logistics center. Shifting this fluctuation risk to external service providers brings short-term relief, but in the long term the service providers will price it in.
This means that employees are deployed as efficiently as possible, but without being “pushed” or “shoved” around. Global competition is reaching new heights, and productivity is the only factor besides quality that keeps TCO at a reasonable level, secures jobs in the region and
prevents a logistics center from being put into operation a few kilometers to the east. Proper planning and control is the key to this.
3. The planning phases
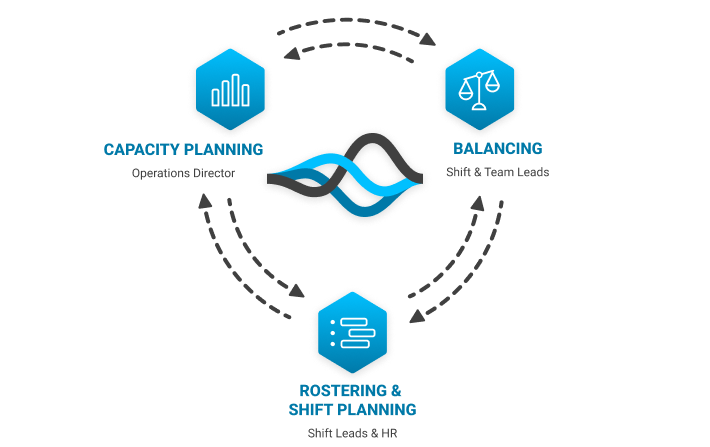
The typical personnel planning cycle begins with strategic capacity/volume/resource planning. The logistics center volume for the coming months or the coming fiscal year is planned, e.g. how many customer orders are expected and what this means in terms of average working hours or full-time equivalents. This rough plan is then usually broken down into a period or weekly plan, i.e. how many full-time equivalents are required per period or week. The rosters, which define the working hours and shifts per employee, are derived from this anonymous planning.
The final level of refinement is the daily hours profile, if this planning level is possible at all: at what times in which shifts (e.g. Mondays between 8:00 and 11:00) will how many full-time equivalents be needed at which station? This planning level is of course desirable, as it facilitates planning ahead as best as possible for the permanent, full-time employees. For example, requirements can be considered such as 50 people in order picking between 8:00 and 11:00 on Mondays during Black Week and 40 people in dispatch between 16:00 and 18:00. The employees also benefit considerably from this kind of planning, as they know exactly when they are assigned to which activity, thus reducing uncertainty and stress.
Why is this planning stage so rarely achieved? Because the relevant planning data is not available. Very good and detailed forecasts would be necessary for this.
4. Balancing on the tightrope
Regardless of the various planning stages, the reality of logistics centers is that operations are always highly reactive, requiring the ability to react to changes in volume, absences, breakdowns, technical problems, etc. at any time, preferably without having to rely on calls,
chance, and intuition. This balancing, i.e. the equalization of resources between work areas depending on the available volume, becomes the core process when making the best possible use of the employees scheduled for eight hours. Many logistics centers work according to the principle of "we know it when it hits us". A fact-based, well-founded, comprehensible, and real-time response to these volatilities is key to achieving employee efficiency and therefore attractive TCO.
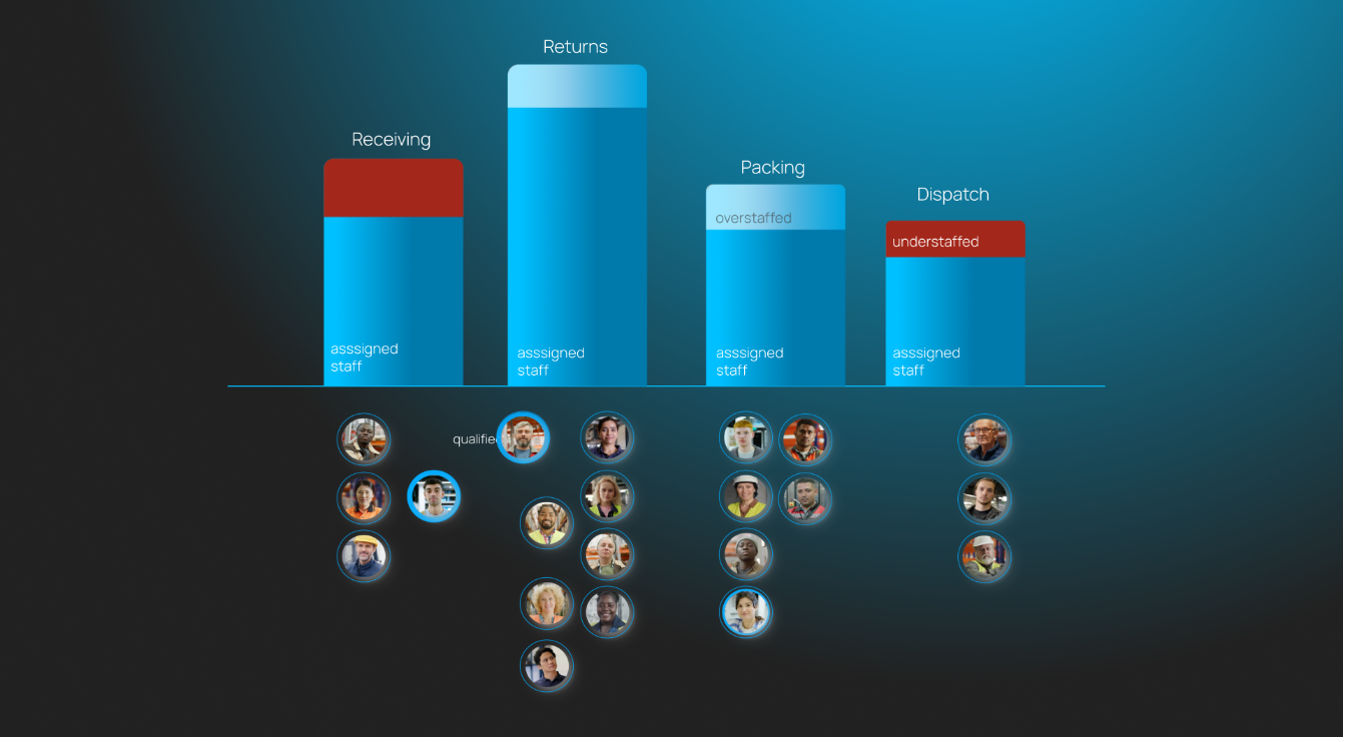
5. Sad but true: Excel, Excel, Excel
Very often, however, it involves a good dose of randomness and intuition. Long-term volume planning, medium-term resource planning and daily balancing are carried out using tools that are rather unsuitable in 2024: Excel, whiteboards with magnets and paper lists. Everyone is aware that although Excel is a flexible universal tool, it is extremely poor for comprehensible, multi-user personnel management. It encourages errors, impairs transparency, makes it impossible to see connections and the overall picture and traceability over the last few months or years. It means the loss of a treasure trove of data.
Why is Excel used when there are numerous tools for personnel management, time recording and shift planning? It is because these tools do not cover the specific warehouse processes very well. They are designed, for example, to calculate salaries at the end of the month or to record all sick leave and vacations, but not to control the volatile warehouse personnel flow processes better. Other tools are generalists that are used in all kinds of industries, from tourism and healthcare to production. Due to their breadth, they lose their specificity. Some WMS offer modules for workforce scheduling, but these are locked into the ecosystem of the respective WMS.
All in all, this means that the entire planning cycle, from strategic planning to daily balancing, is not sufficiently supported digitally. This closes the vicious circle: the lack of digital support means that the data needed to make better predictions in the future and improve the planning phases is missing.
6. Predictions und prescriptions
As shown above with the "planning cycles", being able to plan down to the period and weekly level in daily profiles would be advantageous. By knowing how the resources in the warehouse balance throughout the day, planning with fewer staff or higher performance would be possible and thus reduce the TCO.
As many homemade Excel or even analog PEP solutions are still used in practice, it is difficult to collect the corresponding treasure trove of data, which could be used to generate appropriate long-term and short-term forecasts and prescriptions in the future.
Assuming all this valuable information lost through Excel would be available in a "real" IT system, e.g.
- Employee information
- Working hours, shift models, shift cycles
- Long-term absences
- Skills, training
- Long-term capacities/volumes and daily volumes
- Reactive employee transfers ("five employees borrowed due to increased workload")
- Longer-term employee transfers ("colleague works all week at workstation 3 instead of 5"
- Logbook: "A8 closed, therefore 3 trucks did not show up."
This can be used to calculate fact-based profiles or patterns based on real data:
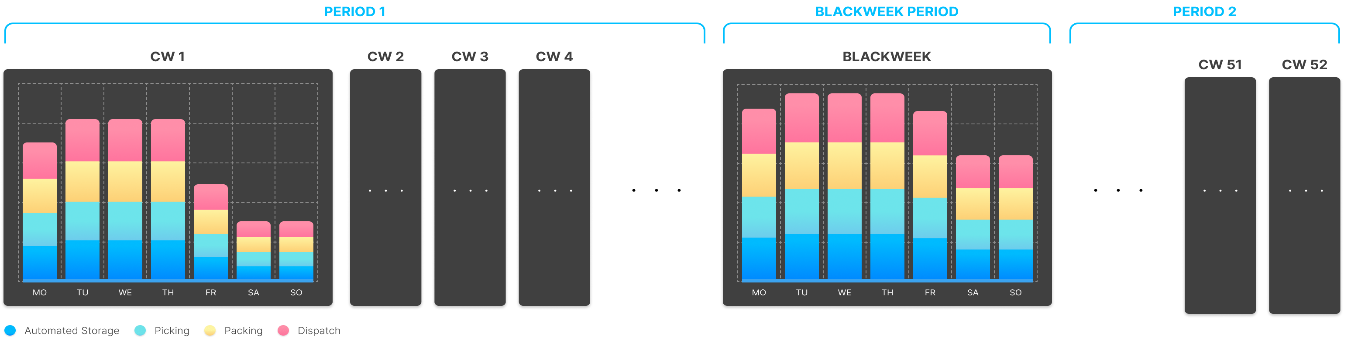
For example: What did the Monday profile look like during the last Black Week?
Two types of forecasts can then be created from these profiles:
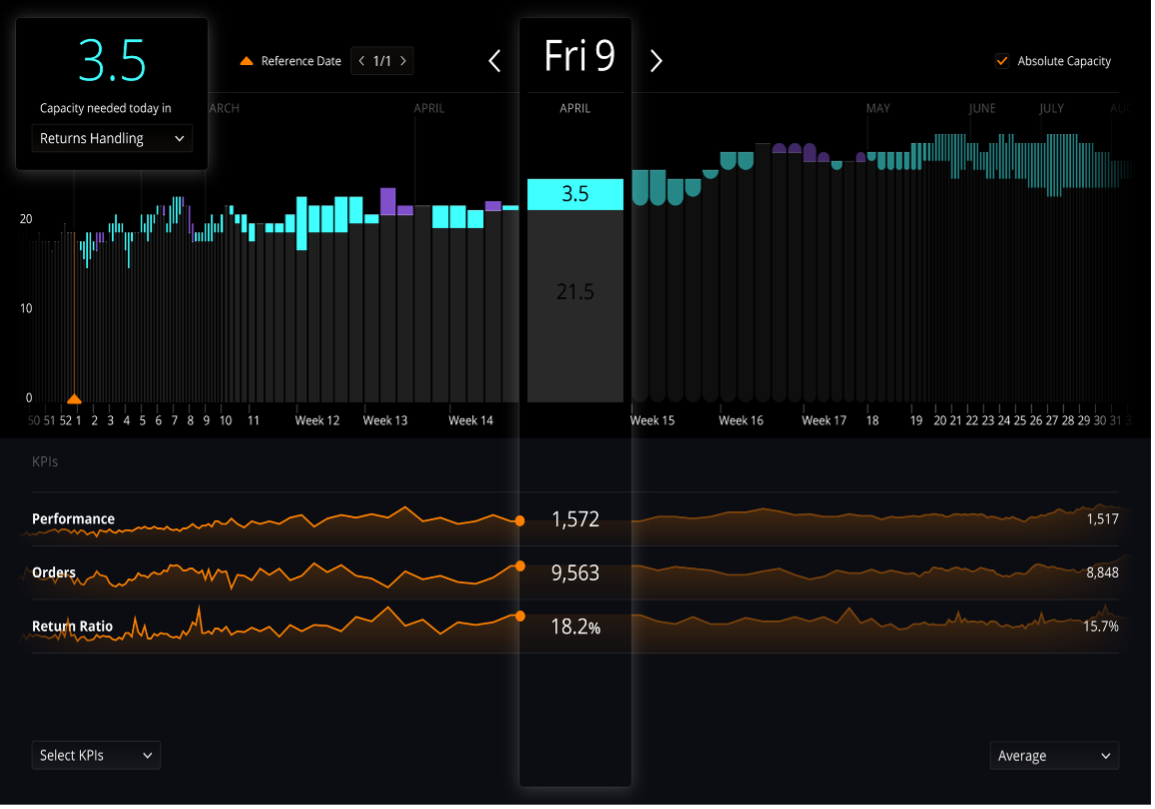
The known profiles are combined with additional information (e.g. the sales forecast) and thus provide a good indication of the capacities required in the longer term.
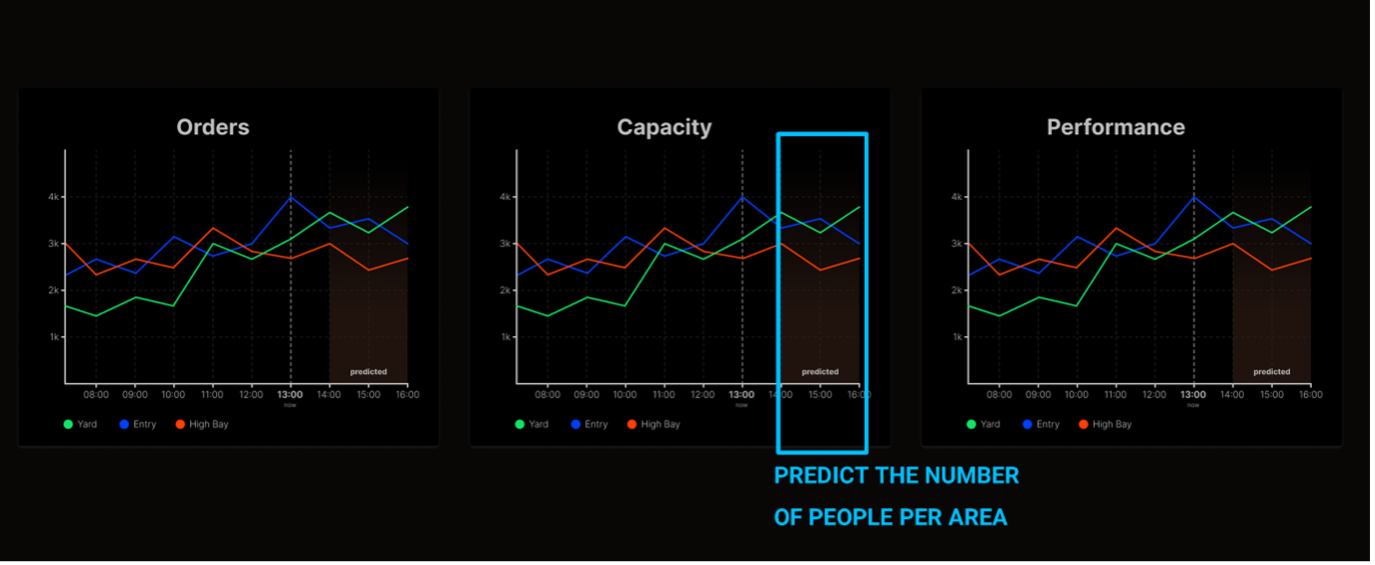
The information from the respective daily profiles is combined with current near-real-time data (e.g. a released wave with several orders and order lines) to create a forecast for the rest of the day.
7. Summary
The digitalization of the personnel planning and control cycle is the key to efficient employee deployment in the logistics center. It is also a prerequisite for realistic forecasts and predictions. As current tools are not designed for this and are therefore far from sufficient, new approaches are needed.